RapidFormRCA
Jump to
RapidFormRCA is the central knowledge hub and go to facility for all 3D printing and scanning requirements within the College.
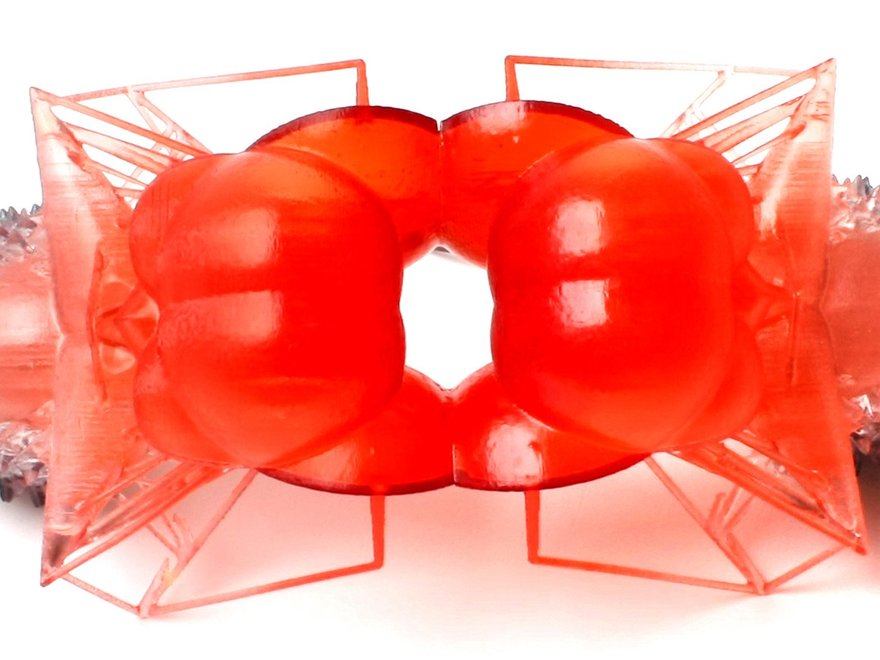
The aesthetic of Fears , Dorry Hsu, Clear resin print rapid prototyping model
For over a decade we have led the way as an ‘equal access for all facility’ offering not only one of the broadest selections of production quality 3D Printing/Additive Manufacturing processes within any academic institution but also bespoke drop-in and one-to-one support and consultancy for academic projects across the entirety of the RCA.
With a history of working with external partners on academic collaborations, museum projects and projects for local enterprises, RapidformRCA actively supports emerging talent and business through its bureau service, available to all alumni, academic staff and research projects.
We welcome proposals for consultation with our technical specialists from all creative fields, including fine art, design, architecture, conservation, medicine and engineering.
Technologies currently in use include high-end prototyping equipment from Stratasys, 3D Systems and Solidscape, as well as high-definition and colour 3D Scanning from Artec.
Alumni access to RapidFormRCA
Alumni are eligible to access RapidFormRCA bureau service at a discounted rate. RapidFormRCA offers high-end 3D printing, 3D scanning and software processes for digital, and physical rapid prototyping and making.
Contact RapidformRCA
To find out more, or to get in touch about a project, email us at
rapidform@rca.ac.uk
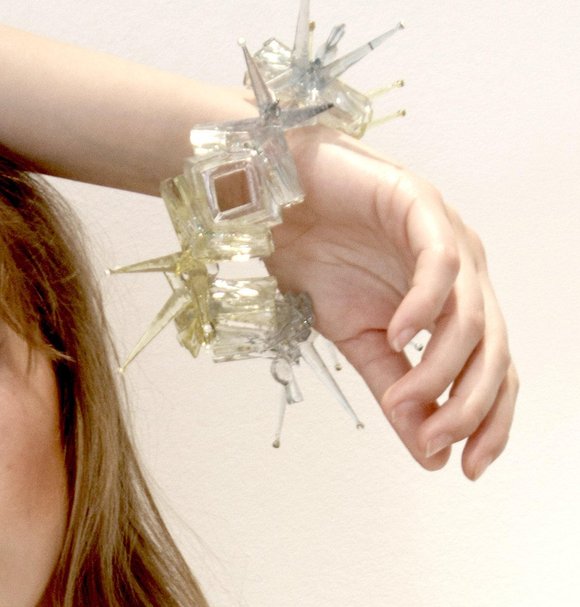